Compressed Air Lines
Condition Monitoring of COMPRESSED AIR Lines
Our Product: We take annual contracts of inspection of the pipelines for leakages wherein the frequency of inspection may be monthly, quarterly or half yearly and the corrective action may also be a part of the contract. The rates will depend upon the tenure of contract and exclusive discounts will be available for five year contracts.
Procedure:
The visits will be scheduled as per the customer’s suitability and the number of visits will have to be decided by customer. The annual charges will depend on the number of visits per annum.
Our Product: We take annual contracts of inspection of the pipelines for leakages wherein the frequency of inspection may be monthly, quarterly or half yearly and the corrective action may also be a part of the contract. The rates will depend upon the tenure of contract and exclusive discounts will be available for five year contracts.
Procedure:
The visits will be scheduled as per the customer’s suitability and the number of visits will have to be decided by customer. The annual charges will depend on the number of visits per annum.
-
Evaluation : You have to identify the misuse or poor applications for compressed air in which leaks are to be traced. You entrust us the investigation of your identified applications.
-
Detection : We mutually schedule a visit and our expert will visit you with SDT270 ultrasound equipment to execute the survey. Using ultrasound technology, our experts will pin-point where you are leaking compressed air
-
Identification : We shall mark all such areas with tags for identification purpose.
-
Tracking : We shall submit our survey report and suggest you to fix the leaks or if in contract we will fix the leaks.
-
Verification : You shall ensure that the leaks are fixed, incase if repair is in your scope and the system’s performance has improved.
-
Re-evaluation : If asked upon by you, we shall re-inspect your compressed air system post fixation of leaks and that will be charged extra or if the repairs are under or scope we will re-check and confirm the corrective actions.
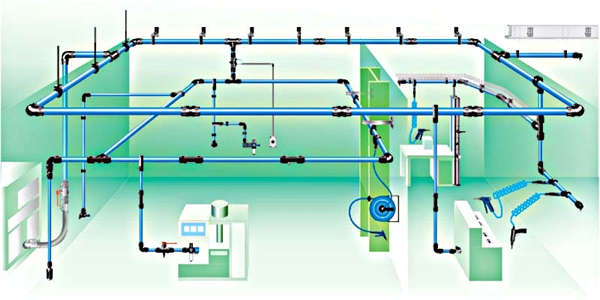
Preface:
Leaks can form practically anywhere in a plant. This includes pressurized systems and systems under a vacuum. Leaks can occur internally through valves and steam traps, in heat exchanger and condenser tubes or to atmosphere.
Immaterial of what many think, compressed air is not free and loss of gases through leaks costs industries lots of money. It is also important to locate potential safety hazards from leaks. This can be overcome through establishing a compressed air leak survey program.
Leaks can be a significant source of wasted energy in an industrial compressed air system, sometimes wasting 20-30% of a compressor’s output. A typical plant that has not been well maintained will likely have a leak rate equal to 20% of total compressed air production capacity.
On the other hand, proactive leak detection and repair can reduce leaks to less than 10% of compressor output.
In addition to being a source of wasted energy, leaks can also contribute to other operating losses. Leaks cause a drop in system pressure, which can make air tools function less efficiently, adversely affecting production. In addition, by forcing the equipment to cycle more frequently, leaks shorten the life of almost all system equipment (including the compressor package itself). Increased running time can also lead to additional maintenance requirements and increased unscheduled downtime. Finally, leaks can lead to adding unnecessary compressor capacity.
While leakage can come from any part of the system, the most common problem areas are:
Leaks can form practically anywhere in a plant. This includes pressurized systems and systems under a vacuum. Leaks can occur internally through valves and steam traps, in heat exchanger and condenser tubes or to atmosphere.
Immaterial of what many think, compressed air is not free and loss of gases through leaks costs industries lots of money. It is also important to locate potential safety hazards from leaks. This can be overcome through establishing a compressed air leak survey program.
Leaks can be a significant source of wasted energy in an industrial compressed air system, sometimes wasting 20-30% of a compressor’s output. A typical plant that has not been well maintained will likely have a leak rate equal to 20% of total compressed air production capacity.
On the other hand, proactive leak detection and repair can reduce leaks to less than 10% of compressor output.
In addition to being a source of wasted energy, leaks can also contribute to other operating losses. Leaks cause a drop in system pressure, which can make air tools function less efficiently, adversely affecting production. In addition, by forcing the equipment to cycle more frequently, leaks shorten the life of almost all system equipment (including the compressor package itself). Increased running time can also lead to additional maintenance requirements and increased unscheduled downtime. Finally, leaks can lead to adding unnecessary compressor capacity.
While leakage can come from any part of the system, the most common problem areas are:
-
Couplings, hoses, tubes, and fittings,
-
Pressure regulators,
-
Open condensate traps and shut-off valves, and
-
Pipe joints, disconnects, and thread sealants.
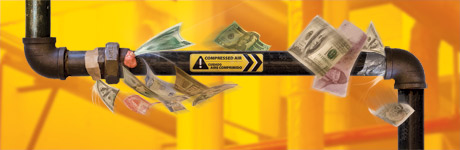
How to Fix Leaks
Leaks occur most often at joints and connections. Stopping leaks can be as simple as tightening a connection or as complex as replacing faulty equipment such as couplings, fittings, pipe sections, hoses, joints, drains, and traps. In many cases leaks are caused by bad or improperly applied thread sealant. Select high quality fittings, disconnects, hose, tubing, and install them properly with appropriate thread sealant.
Non-operating equipment can be an additional source of leaks. Another way to reduce leaks is to lower the demand air pressure of the system.
Leaks occur most often at joints and connections. Stopping leaks can be as simple as tightening a connection or as complex as replacing faulty equipment such as couplings, fittings, pipe sections, hoses, joints, drains, and traps. In many cases leaks are caused by bad or improperly applied thread sealant. Select high quality fittings, disconnects, hose, tubing, and install them properly with appropriate thread sealant.
Non-operating equipment can be an additional source of leaks. Another way to reduce leaks is to lower the demand air pressure of the system.